A vacumetro, also known as a vacuum gauge, is a device used to measure and monitor vacuum pressure levels in various industrial and scientific applications.
This article delves into various types of vacuum gauges, shedding light on their functionalities and applications to comprehensively understand these crucial instruments.
Different Types of Vacuum Gauges
High Vacuum Gauges
High vacuum gauges are specialized instruments tailored to measure pressure levels ranging from 10^-3 to 10^-9 Torr.
Widely deployed in research laboratories, manufacturing facilities, and environments requiring ultra-low pressure measurements, these gauges employ advanced technologies like ionization and thermal conductivity to furnish accurate and precise pressure readings.
Inverted Oil Gauges (Manometers)
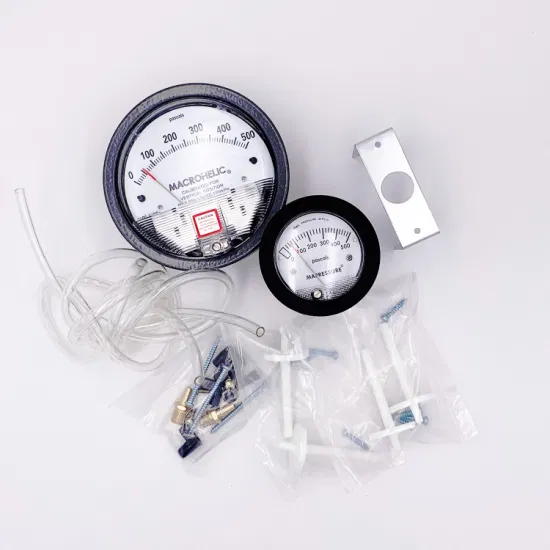
Inverted oil gauges, called manometers, offer a straightforward yet reliable approach to measuring pressure levels between 10^-3 to 10^-5 Torr. Consisting of a U-shaped tube filled with oil and connected to the vacuum system, these gauges utilize changes in oil levels to gauge pressure alterations within the system.
Mechanical Gauges (Bourdon Tube Gauges)
Mechanical gauges, also known as Bourdon tube gauges, are widely adopted vacumetros operating on the principle of mechanical deformation of a metal tube.
They excel in measuring pressure levels from atmospheric pressures down to 10^-3 Torr, prized for their robustness, simplicity, and cost-effectiveness.
Cold and Hot Cathode Ionization Gauges
Cold and hot cathode ionization gauges are highly sensitive vacumetros catering to pressure measurements ranging from 10^-10 to 10^-4 Torr.
Relying on ionizing gases within the vacuum system, these gauges generate electrical currents proportional to pressure levels, making them indispensable for sophisticated scientific research and high-vacuum applications.
Capacitance Diaphragm Gauges (CDM Gauges)
Capacitance diaphragm gauges, or CDM gauges, represent highly accurate and reliable vacumetros designed for precise pressure measurements.
Leveraging changes in capacitance resulting from diaphragm deflection under vacuum pressure, these gauges find extensive utility in semiconductor manufacturing, thin film deposition, and other applications mandating precise vacuum control.
Pirani Gauges
Pirani gauges emerge as widely embraced vacumetros renowned for their simplicity, cost-effectiveness, and high accuracy within the pressure range of 10^-3 to 10^-2 Torr.
Operating on the principle of measuring the thermal conductivity of gases, these gauges detect pressure variations by monitoring temperature shifts in a heated filament, with filament resistance alterations facilitating pressure level determination.
Best Practices For Safe Operation Of Vacuum Gauges
Vacuum gauges, or vacumetros, are indispensable tools across various industries to measure and monitor vacuum pressure levels. While these devices offer substantial benefits, ensuring safety during operation is paramount.
Importance Of Following Safety Protocols
Prioritizing safety when operating vacuum gauges is essential to minimize the risk of accidents, injuries, and equipment damage. Adherence to safety protocols creates a secure working environment and safeguards the well-being of personnel. To uphold safety standards, consider the following guidelines:
- Wear appropriate personal protective equipment (PPE) such as gloves, safety glasses, and lab coats to protect against potential hazards.
- Familiarize yourself with the manufacturer’s instruction manual before operating the vacuum gauge to ensure proper usage.
- Regularly inspect the vacuum gauge to detect any signs of damage or malfunction and address them promptly.
- Ensure that only trained and authorized personnel operate the vacuum gauge to mitigate the risk of misuse or accidents.
- To maintain a safe working environment, adhere to all relevant workplace safety guidelines and regulations.
Potential Hazards Associated With Vacuum Systems
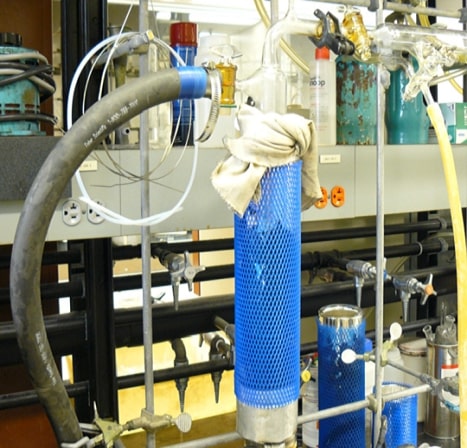
Understanding the potential hazards of vacuum systems is crucial for preventing accidents and injuries. Here are some common risks associated with vacuum gauges:
- Pressure-related incidents: Vacuum systems can generate high-pressure levels, leading to explosions or implosions if not appropriately managed.
- Chemical exposure: Vacuum systems used in environments with hazardous chemicals pose chemical exposure risks, resulting in health hazards if not handled correctly.
- Electrical hazards: Vacuum gauges may contain electronic components that pose electrical risks if mishandled or improperly connected.
- Mechanical hazards: Improper maintenance or operation of vacuum gauges can lead to mechanical failures such as leaks or fractures, causing injury or equipment damage.
- Cryogenic risks: Certain vacuum systems utilize cryogenic substances, which can be extremely cold and pose risks of frostbite or other injuries if mishandled.
Step-by-step Guide On Using A Vacuum Gauge Effectively
System Preparation
Ensure that the system intended for vacuum measurement is adequately prepared. This involves sealing any openings and verifying that the system is free from leaks.
Gauge Connection
Connect the vacuum gauge to the pressure port of the system using suitable tubing or fittings. Ensure that all connections are tight and any inline valves are fully open.
Reading Acquisition
Initiate the system and observe the reading displayed on the vacuum gauge. Take note of the stable reading obtained and compare it against the system’s specifications or the expected value for the particular application.
Result Interpretation
Utilize the vacuum level to diagnose potential issues or confirm the system’s correct operation. If the reading deviates from expectations, further investigation should be conducted to pinpoint the underlying cause.
Safety Measures To Protect Personnel And Equipment During Vacuum Gauge Operation
Safety Measure | Description |
Proper Ventilation | Ensure that the area where the vacuum system operates has sufficient ventilation to prevent the accumulation of hazardous gases or vapors. |
Regular Equipment Inspection | Conduct routine inspections of the vacuum gauge to identify any indications of damage, leaks, or malfunctions. Take prompt action to address any issues found. |
Training and Competency | Provide thorough training to personnel operating the vacuum gauge, ensuring they possess the necessary knowledge and skills to handle the equipment safely. |
Safe Handling of Chemicals | Establish stringent protocols for safely storing, handling, and disposing hazardous chemicals when working with vacuum systems. |
Emergency Procedures | Establish clear and accessible emergency procedures, including evacuation routes and equipment shutdown protocols, to be followed in case of an incident. |
Implementing these safety measures significantly reduces the potential risks associated with vacuum gauges, ensuring a safe working environment for all personnel involved.
Key Considerations For Selecting Vacuum Gauges
Several essential factors merit consideration when choosing the appropriate vacuum gauge for your requirements. By thoroughly assessing these factors, you can ensure the selection of a vacuum gauge that aligns precisely with your application needs in terms of accuracy and precision.
Specific Application Requirements
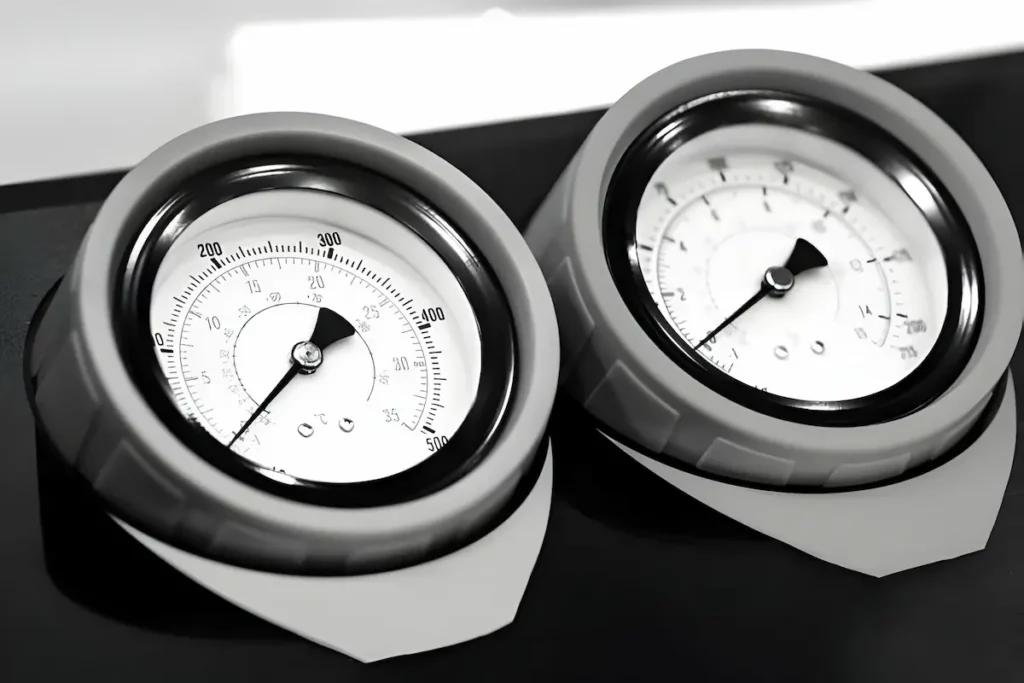
Understanding the unique requirements of your application is paramount in selecting a suitable vacuum gauge.
Each application may present distinct demands, necessitating a vacuum gauge capable of accommodating specific pressure ranges, temperature ranges, and gas types prevalent in your operational environment, whether a laboratory, industrial facility or other settings.
Range And Sensitivity Of The Vacuum Gauge
Opting for a vacuum gauge with an appropriate range and sensitivity is crucial for precisely measuring and monitoring vacuum levels.
The range denotes the lowest and highest pressures the indicator can accurately measure, while sensitivity determines the precision and detail of the measurements. Choosing a range and sensitivity of a vacuum gauge that aligns with your application’s requirements ensures accurate readings.
Compatibility With Pressure Measurement Units
Another vital factor to consider is the compatibility of the vacuum gauge with various pressure measurement units.
Different applications may necessitate diverse pressure units such as Pascal (Pa), Torr, or Millibar. Selecting a vacuum gauge that supports the required units of measurement facilitates easy interpretation and comparison of readings, enhancing operational efficiency.
Budgetary Considerations
Budget considerations play a significant role in the selection process of vacuum gauges. Establishing a budget constraint beforehand lets you streamline your options and focus on gauges within your financial reach.
While adhering to budgetary constraints, it is essential to balance cost and quality. Investing in a reliable and accurate vacuum gauge is necessary for the efficacy and success of your application.
Common Mistakes To Avoid When Using Vacuum Gauges
- Avoid exceeding the maximum rated pressure of the gauge, as it can damage the bourdon tube or cause leaks. Start the system at low pressure and gradually increase while monitoring the gauge.
- Select a vacuum gauge specifically designed for the type of pressure you are measuring, whether absolute, differential, or relative.
- Avoid improper connection to the system, leading to leaks and inaccurate readings. Always use the correct fittings and verify tight connections.
Troubleshooting Common Issues With Vacumetros
When using vacumetros, users may encounter various issues affecting their performance and accuracy. Here are some common problems you might face and their corresponding solutions:
- The Vacumetro Does Not Power On
- Check if the batteries are correctly installed and fully charged.
- Replace the batteries if needed.
- Ensure that the power switch is in the correct position.
- Inaccurate Readings
- Verify the connection between the vacumetro and the system being measured.
- Check if the vacumetro is calibrated correctly.
- Clean the sensor and ensure it’s free from any obstructions.
- Minimize external factors interfering with the readings, such as temperature variations or air drafts.
- The Vacumetro Is Not Responding to Buttons
- Ensure that the buttons are not stuck or dirty.
- Clean the buttons gently with a soft cloth or compressed air to remove debris.
- Refer to the user manual for specific troubleshooting instructions.
Troubleshooting Techniques For Accurate Readings
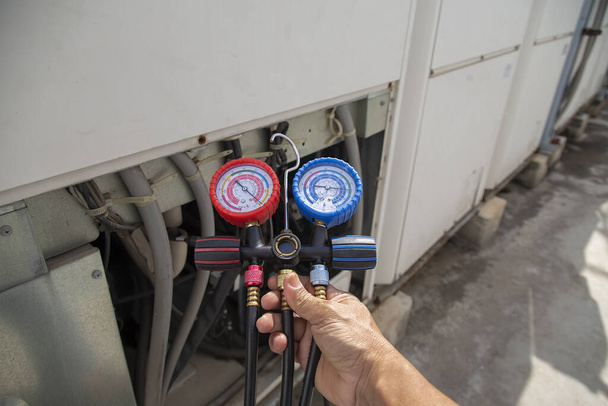
To maintain accuracy with your vacumetros, consider these troubleshooting techniques:
- Ensure the vacumetro is correctly connected to the system being measured. Loose or improper connections can lead to inaccurate readings.
- Periodically verify the calibration of your vacumetro and recalibrate if needed. Calibration drift can affect measurement accuracy over time.
- Keep the sensor clean and clear of any obstructions or debris. A dirty sensor can compromise measurement accuracy.
- Prevent interference by avoiding the placement of the vacumetro near strong magnetic fields or electrical equipment, which can disrupt readings.
- If applicable to your vacumetro model, utilize temperature compensation techniques to account for temperature variations and maintain accuracy.
Frequently Asked Questions:
1. How Do Vacumetros Work?
Vacumetros operate based on different principles such as ionization, thermal conductivity, mechanical deformation, capacitance changes, and thermal conductivity of gases, depending on the gauge type.
2. What Factors Should Be Considered When Choosing A Vacumetro?
Factors to consider include the specific application requirements, range and sensitivity of the vacuum gauge, compatible pressure measurement units, and budget constraints.
3. How Should Vacumetros Be Used Safely?
To use vacumetros safely, it’s essential to follow proper protocols, wear appropriate personal protective equipment, conduct regular equipment inspections, train personnel, and establish emergency procedures.
4. What Are Some Common Mistakes To Avoid When Using Vacumetros?
Common mistakes to avoid include over-pressurizing the gauge, using the wrong gauge type, and incorrect attachment to the system.
5. What Are The Future Trends And Advancements In Vacumetros?
Future advancements in vacumetro technology are expected to enhance their performance and usability, enabling more precise and reliable vacuum pressure measurements across various applications.
Conclusion:
In conclusion, vacumetros are crucial in various industries and scientific fields because they accurately measure vacuum pressure levels. By understanding the different types of vacumetros available, adhering to safety measures, and avoiding common mistakes, users can effectively utilize these tools to ensure the efficiency and safety of vacuum systems. In the future, advancements in vacumetro technology will further enhance their performance and usability, enabling more precise and reliable vacuum pressure measurements across various applications.
Read: